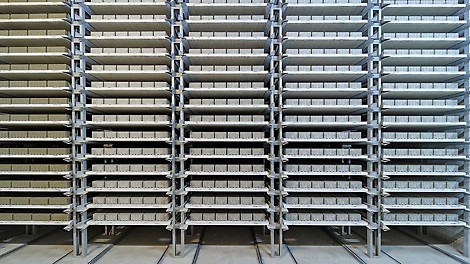
PERI Pave - The production pallet for the paving industry
Less concrete buildup and less cleaning effortThe latest generation of PERI Pave has been continuously refined and now comes with an integrated release effect in its plastic coating. This innovative surface significantly reduces concrete and stone residue buildup on the pallets. Along with its tough, wear-resistant coating, PERI Pave features a strong multiplex hardwood core, offering excellent load-bearing capacity, high surface hardness, and resistance to abrasion. It also delivers uniform vibration performance, all while keeping its own weight low.
These qualities make PERI Pave a perfect choice for producing heavy concrete products or items that require exceptional flatness. It’s also ideal for use in high-humidity environments, such as air-conditioned curing chambers or with washed concrete products.
The structure of the PERI Pave
The multiplex core is produced through the cross-bonding of high-quality hard wood veneers from sustainably managed forests. The polypropylene coating, which has been especially developed for the utilisation in concrete block manufacturing plants, offers particularly high impact and abrasion resistance and thus ensures the longevity of the PERI Pave production pallets.
PERI Pave in action
The low net weight of the PERI Pave production pallet leads to energy savings during the transportation through the machine cycle. Cycle times are reduced as there are no withdrawal plates, so this increases the efficiency of production.
Even under the highest loads, PERI Pave pallets show minimal deflection due to the very load-bearing core. The thickness of the pallets is adjusted to the production conditions of each customer. So even after many years of use, the deflection will not exceed the requested maximum deflection.
Due to the absolutely homogenous construction of the pallet, the bandwidth of compaction tolerances of the concrete products is limited to a minimum, uniform heights and consistencies are the consequence.
The constant properties of the PERI Pave production pallet are maintained over a long period of time – also with high humidity in air-conditioned chambers as well as during the production of washed concrete products.
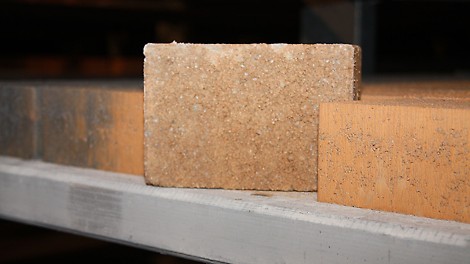
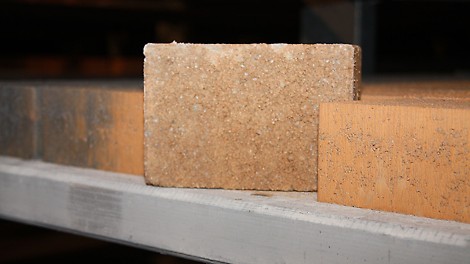
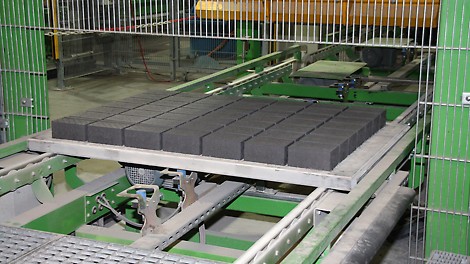
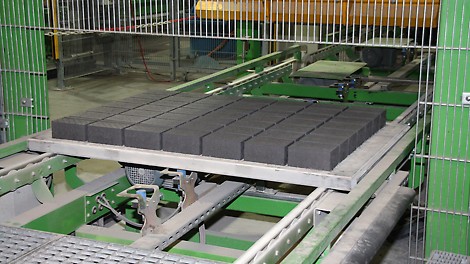
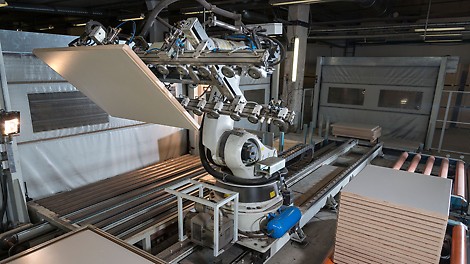
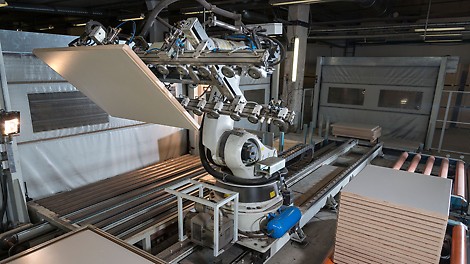
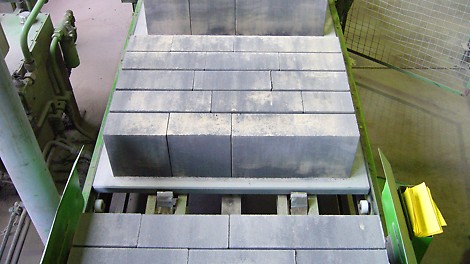
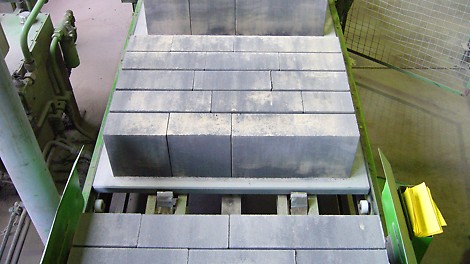
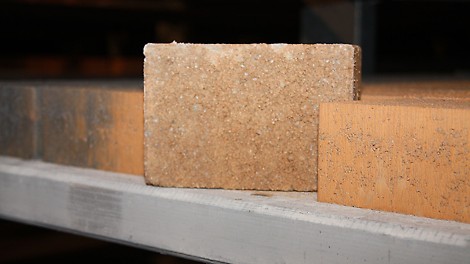
The low net weight of the PERI Pave production pallet leads to energy savings during the transportation through the machine cycle. Cycle times are reduced as there are no withdrawal plates, so this increases the efficiency of production.
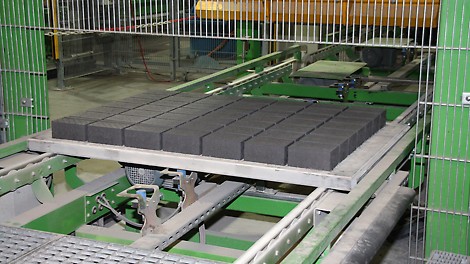
Even under the highest loads, PERI Pave pallets show minimal deflection due to the very load-bearing core. The thickness of the pallets is adjusted to the production conditions of each customer. So even after many years of use, the deflection will not exceed the requested maximum deflection.
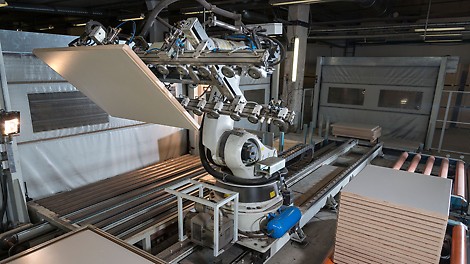
Due to the absolutely homogenous construction of the pallet, the bandwidth of compaction tolerances of the concrete products is limited to a minimum, uniform heights and consistencies are the consequence.
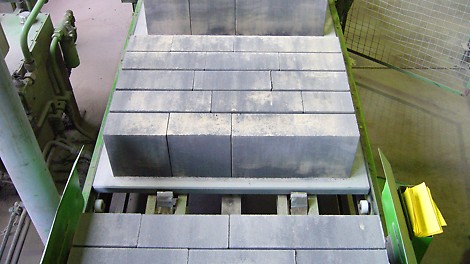
The constant properties of the PERI Pave production pallet are maintained over a long period of time – also with high humidity in air-conditioned chambers as well as during the production of washed concrete products.
Improve the longevity of your PERI Pave panels
PERI Pave ReLife achieves a perfect balance of sustainability and cost-effectiveness. We can professionally recoat the surface of your production board to give them additional service life: resource-saving, cost-effective and still at a high-quality level.
The panels of PERI Pave can continue to be used after the repair with practically no loss of quality. The PERI Pave Repair Kit consists of a router with corresponding tools as well as matching repair patches made of original PERI Pave material.
Since PERI Pave boards move through the entire production cycle alongside the concrete blocks, a close eye is kept on quality throughout the process. Each pallet can be equipped with built-in RFID chips, making it easy to track and monitor quality continuously and reliably.
Cleaning and care extend the service life of the underlay boards. Their unique coating reduces the effort involved. We recommend brushes with plastic bristles to remove any concrete and acrylic residues quickly and thoroughly.
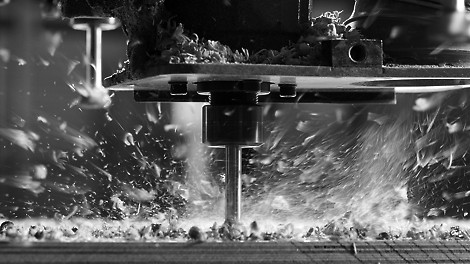
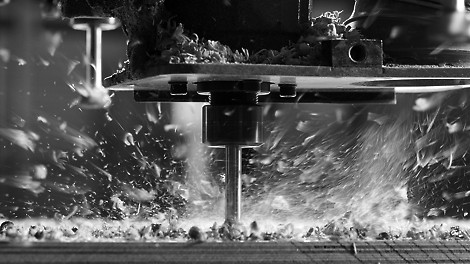
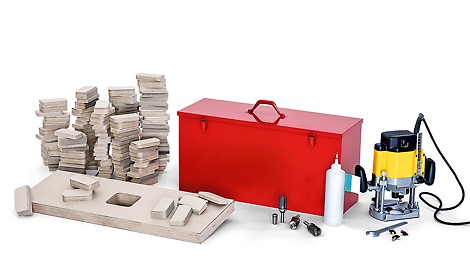
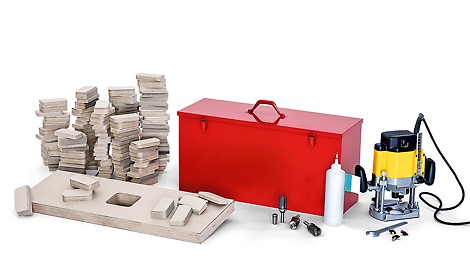
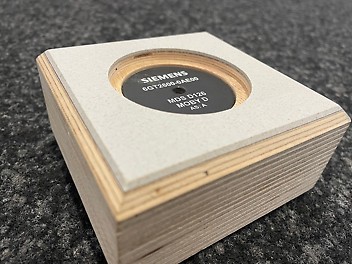
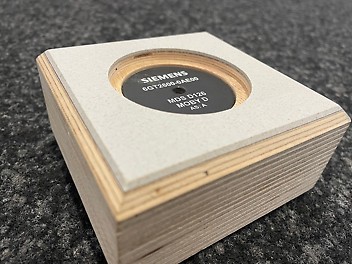


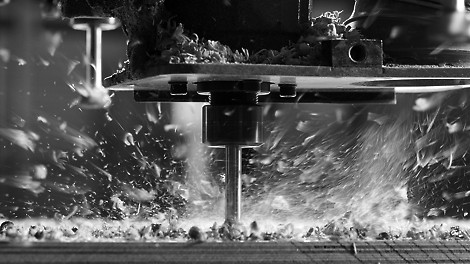
PERI Pave ReLife achieves a perfect balance of sustainability and cost-effectiveness. We can professionally recoat the surface of your production board to give them additional service life: resource-saving, cost-effective and still at a high-quality level.
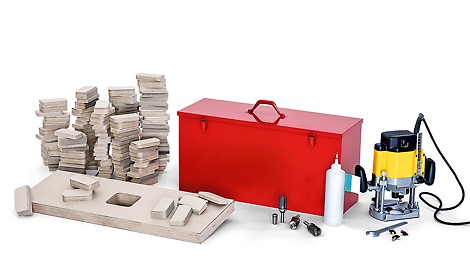
The panels of PERI Pave can continue to be used after the repair with practically no loss of quality. The PERI Pave Repair Kit consists of a router with corresponding tools as well as matching repair patches made of original PERI Pave material.
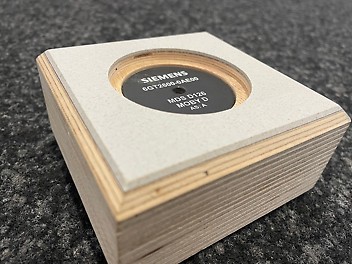
Since PERI Pave boards move through the entire production cycle alongside the concrete blocks, a close eye is kept on quality throughout the process. Each pallet can be equipped with built-in RFID chips, making it easy to track and monitor quality continuously and reliably.

Cleaning and care extend the service life of the underlay boards. Their unique coating reduces the effort involved. We recommend brushes with plastic bristles to remove any concrete and acrylic residues quickly and thoroughly.
Product Data Sheet
Nominal thickness | Format | Weight |
24 – 53 mm | Max. 1500 x 3600 mm | About 740 kg / m³ with wood moisture of about 12% |
Interested in using PERI Pave for your next project?
Call us on 01277 582042 to discuss your requirements further.