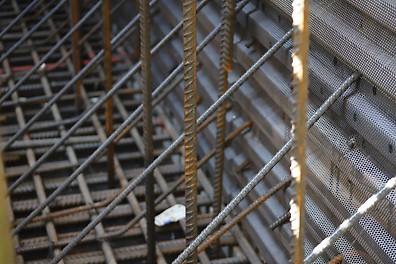
Interested in learning more about BECOSTOP?
Call us on 01788 861600 to discuss your requirements further.
Traditional shuttering would need extensive propping and a supporting frame, which would need to be removed and rebuilt once the pour was complete. Site space was tight, with a live underground railway line neighbouring the basement and work starting on the floor above simultaneously. With limited time and space to build timber shuttering, the John F Hunt project team were looking for a more efficient solution to speed up the concreting process and conserve space on site.
By introducing our permanent stopend solution, BECOSTOP, we were able to reduce the installation time and eliminate the removal process altogether. In partnership with Richter, we provided a full temporary works design inclusive of CAT 2 checks which enabled the site team to achieve a rate of rise of 350mm per hour.
Installation was simplified by using tying wire as a time-saving alternative to clamps when connecting the units to the rebar. By delivering bespoke BECOSTOP shutters to site, the units were ready to assemble from the pallet without any additional cutting or adjustments required – a big advantage considering the site limitations.
The perforations on the mesh effectively minimised grout leakage between pours, while our innovative spacer strip, BECOSPACE, ensured zero grout leakage in the cover zone.
Using permanent stopends also helped to reduce material and save vital workspace on site, as external props were not required.
With BECOSTOP’s key profile, our customer was able to achieve full reinforcement continuity, resulting in stronger construction joints.
Call us on 01788 861600 to discuss your requirements further.